Quality Control
Production system that achieves high quality
KITZ Group’s manufacturing is based on the concept of delivering products when necessary and in the quantities required with better quality.
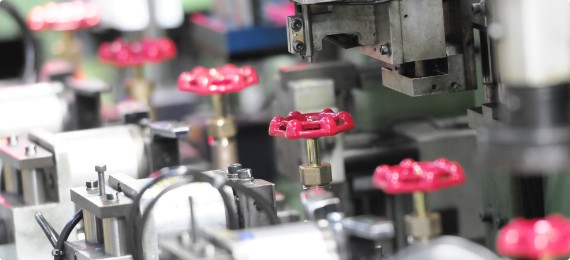
Integrated production system that provides quality control starting from castings
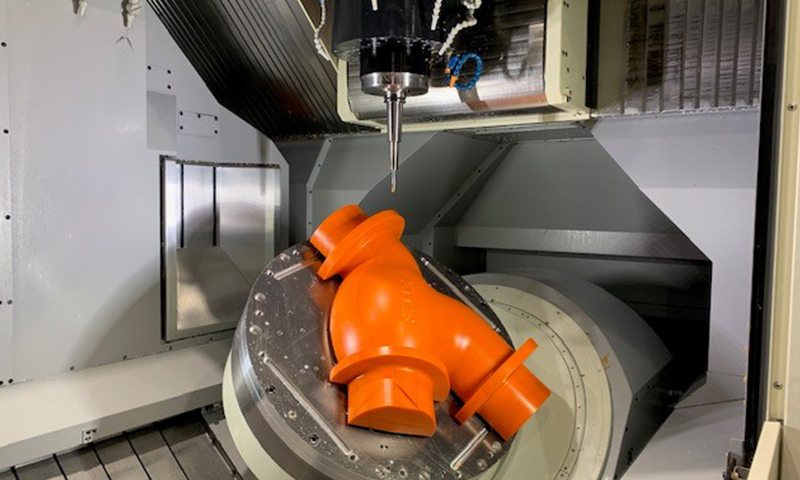
Based on integrated production, the KITZ Group positions castings (forge and foundry materials) that are valve materials as the core technology and produces them internally from castings. We have established an integrated production system in which our Group has its own casting facilities for the main valve materials such as bronze, casting iron, ductile, stainless steel and casting steel, thus putting in place a quality assurance system starting from materials. We also provide a wide variety of products in small quantities.
What supports manufacturing operations based on the market-oriented concept is the production method according to the KITZ Innovative and Challenging System (KICS). KICS provides a mechanism of sending only good products to the subsequent process by producing each product one by one in a sequence of processes at the exact timing with which it can be sold. It also achieves the elimination of stagnation and waste in a series of processes from order receipt to production and delivery. Moreover, we strive to further reduce delivery times and reinforce production lines continuously by thoroughly implementing standard work and improving processes.
In June 2021, a machining center for casting mold production was set up at the Nagasaka Plant. The production of molds, which determine the quality of casted items, requires expertise in molding plan design and the precision machining technologies to give shape to those plans. By accumulating these mold production technologies in-house, we will be able to improve casting quality and shorten mold production lead times.
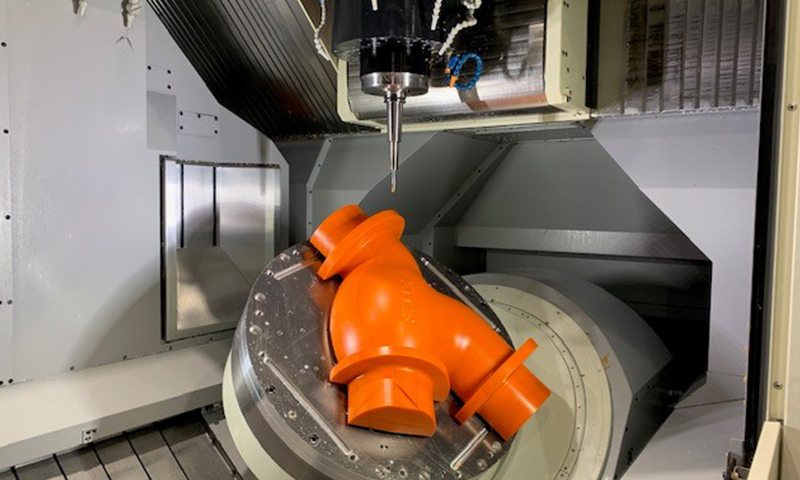
Toward an Eco-friendly Manufacturing Workplace for Creating Added Value
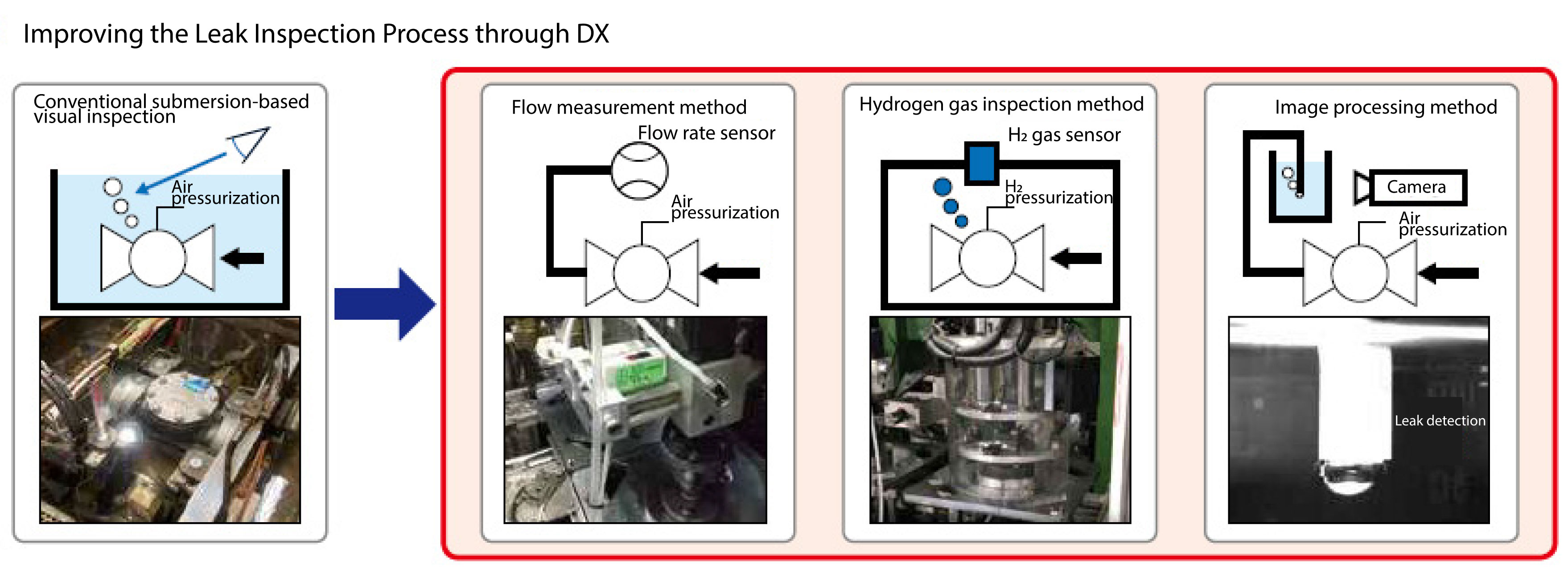
KITZ is investing proactively in R&D for new production technologies and environmental improvements with the aim of achieving quality, prices, delivery times, services and sustainable, eco-friendly production processes that will guarantee the satisfaction of our customers. In addition to introducing robots to the manufacturing workplace, we are also outfitting our production lines with ICT-based equipment management and inspections that apply image processing and sensor technologies. New initiatives include the reuse of sand used in the casting process, the recycling and use of water resources used in valve inspections and the substitution of raw materials in plastic components. Through these initiatives, we are driving the evolution of eco-friendly production processes in the manufacturing workplace toward creating greater added value.
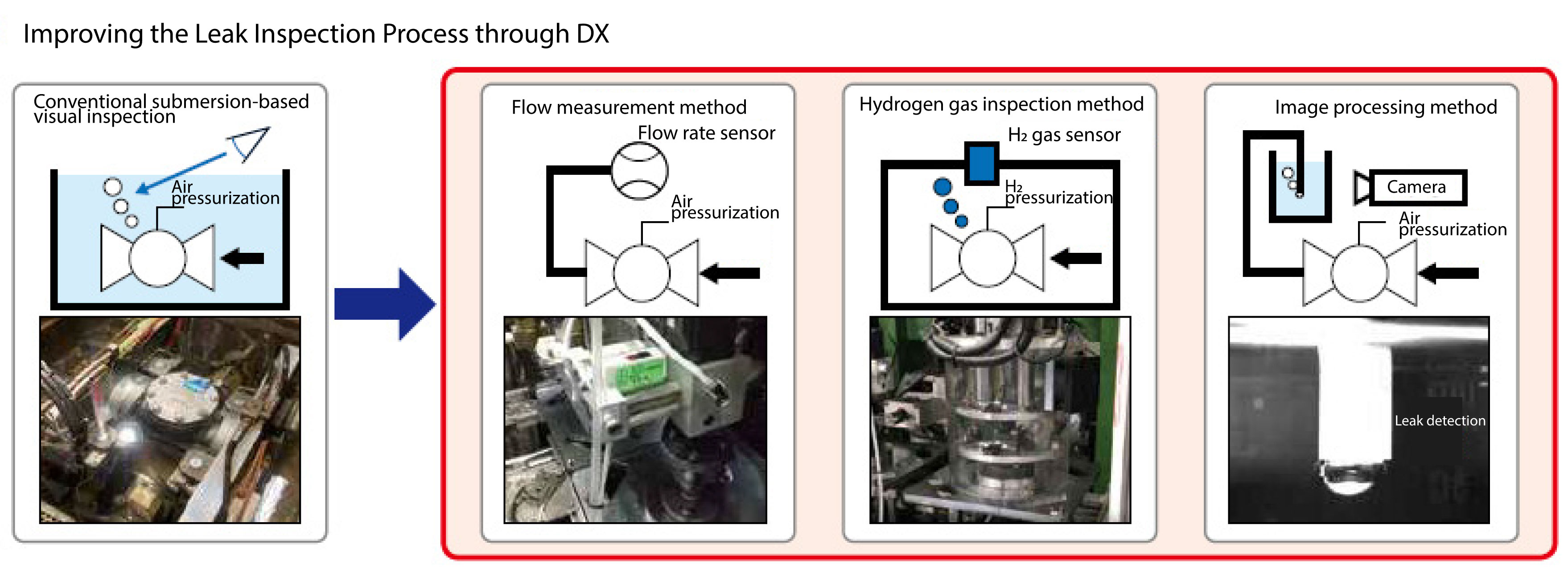
KITZ brand is backed by quality management systems
KITZ Corporation recognized the importance of conformance to the international standard on quality management systems earlier than anyone in the industry. In November 1989, KITZ became the first Japanese company to earn ISO 9001 certification. At present, all domestic and international production bases in the KITZ Group have been certified to this standard. In February 2019, our Group company, KITZ Engineering Service Co., Ltd., became the first in the Group to obtain certification for the scope of “valve maintenance” under the standard. Additionally, in July 2001, KITZ Corporation was certified, for the first time in the valve industry in Japan, in accordance with the Pressure Equipment Directive (PED) for CE marking required for European markets. KITZ plants in Taiwan, Thailand, China, Spain and Germany have subsequently obtained PED certification as well.
In addition to these international quality standards, in Japan, KITZ Corporation is approved by the Minister of Economy, Trade and Industry as an authorized gas tester under the High Pressure Gas Safety Act. It supplies Japan Industrial Standards (JIS) certified products and complies with standards of the Japan Water Works Association (JWWA). KITZ plants in Japan and China are also certified to display the API Monogram of the American Petroleum Institute.
Global production network: Manufacturing facilities located in optimum locations
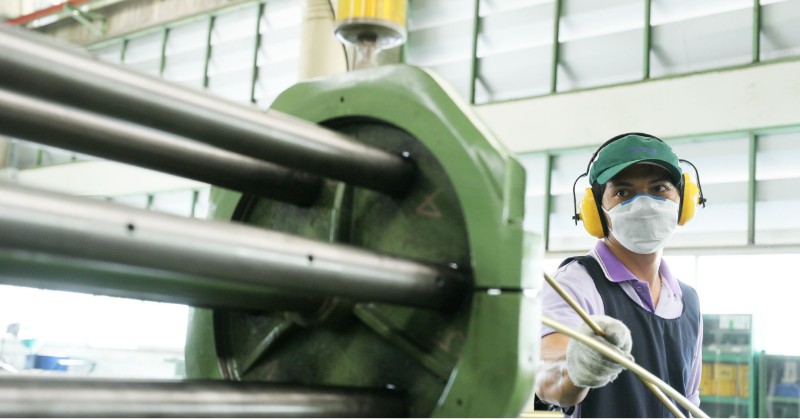
KITZ Group is building a structure for undertaking production in the most suitable locations for its operations around the world.
Under this structure, we produce high value-added products in Japan, while Japan also plays a crucial role as the command center for our global manufacturing activities. The KITZ Group now has international factories in Thailand, Taiwan, China, Korea, India, Spain, Germany and Brazil.
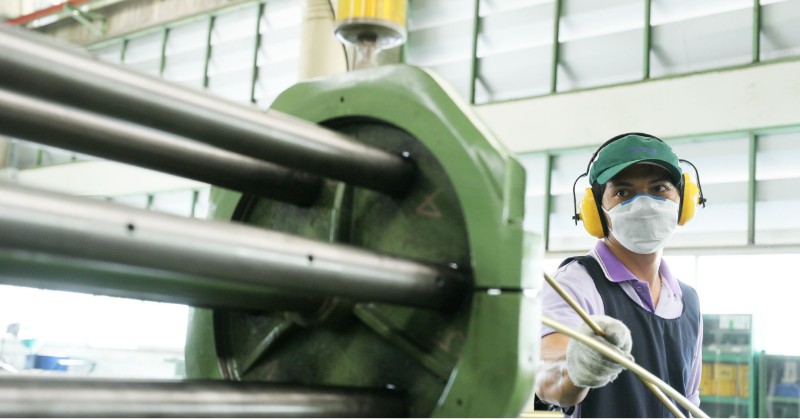
Stainless Steel Valve Manufacturing Process
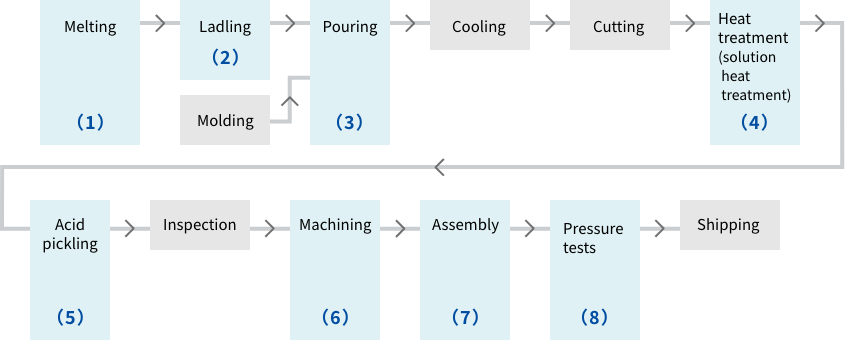
-
- (1) Melting
-
Raw materials are melted in high-frequency electric furnaces.
-
- (2) Ladling
-
Melted metal is ladled for pouring.
-
- (3) Pouring
-
Melted metal is poured into a casting mold. The melted metal flows into the cavity between the upper mold, the lower mold and the core.
-
- (4) Heat treatment (solution heat treatment)
-
Raw materials are quenched after having been heated up to 1,100°C. This process forms a uniform metallic structure and makes mechanical properties such as tensile strength and elongation higher and ensures corrosion resistance.
-
- (5) Acid pickling
-
Pickling castings in acid solution removes impurities such as oxidized scales on the casting surface caused by heat treatment and shot blasting. At the same time, a protective film is formed on the casting surface, enhancing corrosion resistance.
-
- (6) Machining
-
Castings are cut, drilled and processed with machines.
-
- (7) Assembly
-
Various parts and components are assembled to complete valves.
-
- (8) Pressure tests
-
Valves are pressurized with air and/ or water and operated to verify that they satisfy the quality requirement.
Contact us
For inquiries about product technology, product purchases,
catalogs, and quality